In the field of construction reinforcement, the term "rebar adhesive reinforcement" is no stranger to everyone. It is a widely used reinforcement method in recent years. The editor often encounters customers discussing relevant issues about this technology: "Why does the rebar in the rebar adhesive reinforcement come out with a pull? The pull-out test fails!" In response to these phenomena, let's explore and analyze together.
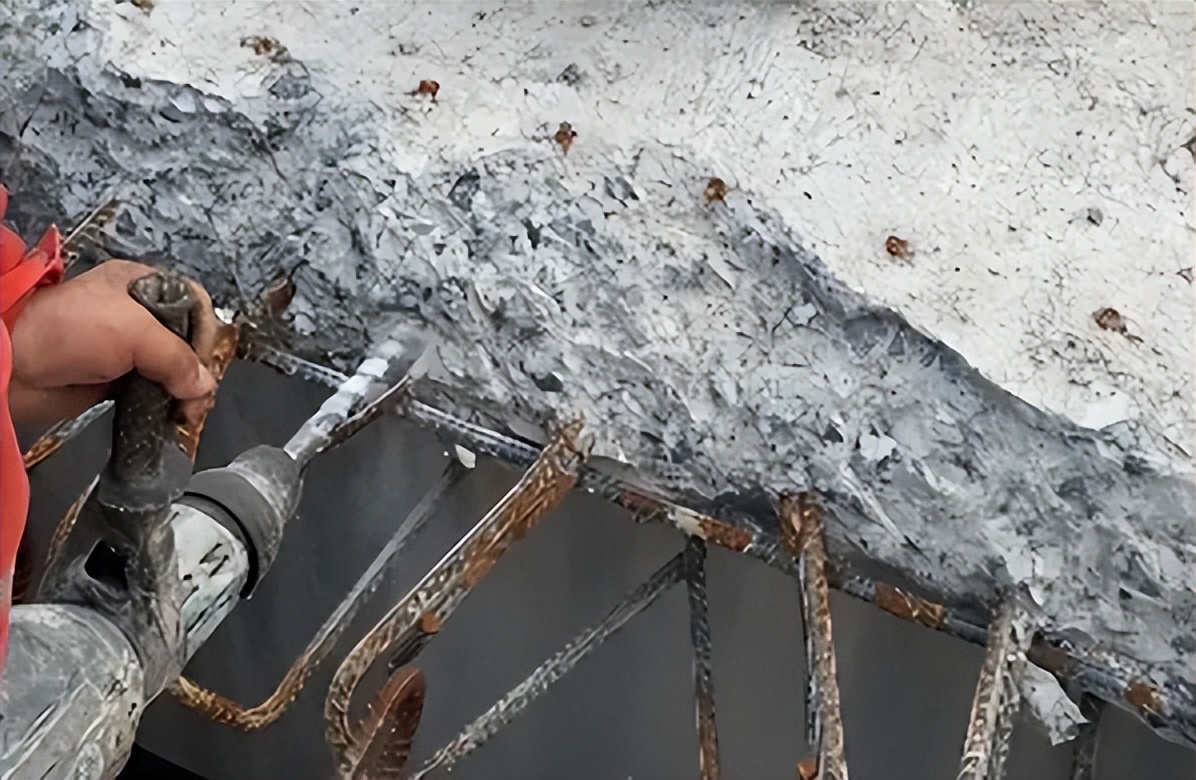
I. Compliance with Construction Regulations
Drilling Holes: Not following design requirements for drilling holes can lead to undersized hole diameters or insufficient drilling depths. Before drilling, it is essential to understand the relevant regulations and ensure that the hole diameter and depth meet the requirements.
Cleaning Holes: Dust or moisture inside the holes must be thoroughly cleaned. Use an air compressor to blow out loose dust and debris from the hole, and clean the hole with a brush to ensure it is dust-free, clean, and dry.
Rust Removal from Rebar Surface: A dirty rebar surface can also affect the outcome. To ensure better results with rebar adhesive, the rebar surface must be rust-free before reinforcement, and it should be cleaned with acetone or alcohol.
II. Adherence to Curing Time Requirements
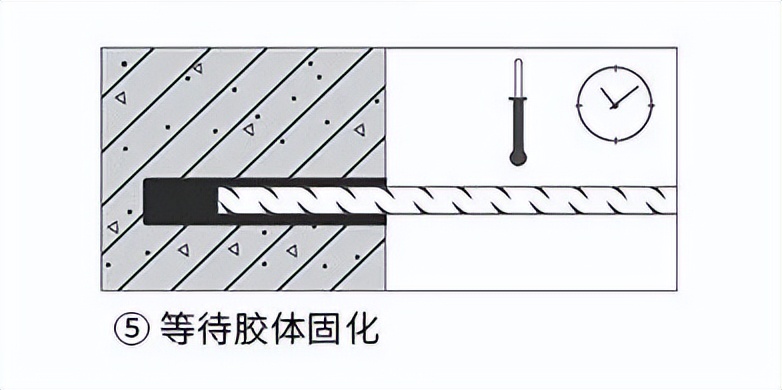
Many people may think that reinforcement is a one-time task and neglect the subsequent curing and maintenance phase, which can affect the anchoring effect of the rebar adhesive.
A colleague of Xiaobang had a personal experience. Once, he went to a construction site to conduct a pull-out test. He installed the rebar in the morning, and in the afternoon, after the adhesive was close to reaching the curing time, he went to the site for the test. However, during the curing process, before it was fully cured, it was subjected to external force. The reason for this was that some workers, to verify if the rebar adhesive had set, would touch the rebar after the installation. In fact, at this point, the rebar adhesive had not fully cured, and touching the rebar would affect its adhesive bonding performance. Since the curing of the adhesive requires a certain amount of time, the pull-out strength will be high after complete curing. The specific curing time should refer to the product instructions from different manufacturers:
III. Use of High-Quality Rebar Adhesive
Even with the same operation steps and curing times, testing with two different types of rebar adhesive can yield vastly different results. When two types of rebar adhesive were tested, one was a common type found on the market, and the other met all the required inspection reports. Both types were used for rebar reinforcement. The result was that the inferior adhesive allowed the rebar to be pulled out easily, failing the pull-out test.
In contrast, the rebar adhesive that met all inspection requirements directly pulled the rebar to the point of breaking during the pull-out test. Therefore, choosing a good product and using the correct method can ensure good performance of the rebar reinforcement, and there is no need to worry excessively about the pull-out test.
IV. Other Factors
Of course, in addition to the points mentioned above that can affect the pull-out effect of the rebar adhesive, there may be other factors:
Temperature and Humidity: The curing process of the rebar adhesive is affected by environmental temperature and humidity. In low-temperature or high-humidity environments, the curing time may be extended, thereby affecting the reinforcement effect.
External Forces: If the rebar adhesive is subjected to significant external forces, such as vibrations or impacts, during the curing period, it may lead to a decrease in the bonding strength between the rebar adhesive and the base material or rebar.
Usage Environment: The rebar adhesive may perform differently in various environments. For example, in corrosive environments, the rebar adhesive may be subject to corrosion, which can affect its reinforcement effect.
To ensure the pull-out effect of rebar adhesive reinforcement, it is necessary to consider the above factors comprehensively and strictly follow the specifications during construction. Pay attention to the curing time, choose high-quality rebar adhesive products, and effectively utilize the performance of rebar adhesive reinforcement!
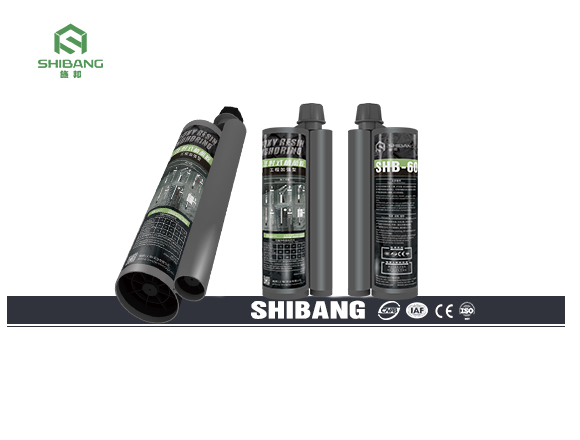
SHB-601 Injected Rebar Adhesive is made from modified epoxy resin, free of any solvents, safe, and non-toxic. It has passed 10 categories and 30 items of testing, meeting the 50-year design life standard. It has strong anchoring force, similar to that of pre-embedded rebar, and easily passes the pull-out test.